Innovating for efficiency using 3D-printing
Innovation is in our genes. We don’t just innovate in our car parks and for the customer’s digital journey, we also innovate behind the scenes. Many of our innovations go unnoticed, yet they do make us more efficient and responsive.
Our engineers and technicians also love to innovate. They are responsible for installing parking and other equipment in our facilities, and for maintaining these installations to keep our car parks open. If something gets damaged or stops working, one of our maintenance crew drives to the car park to repair technical faults and fix breakdowns.
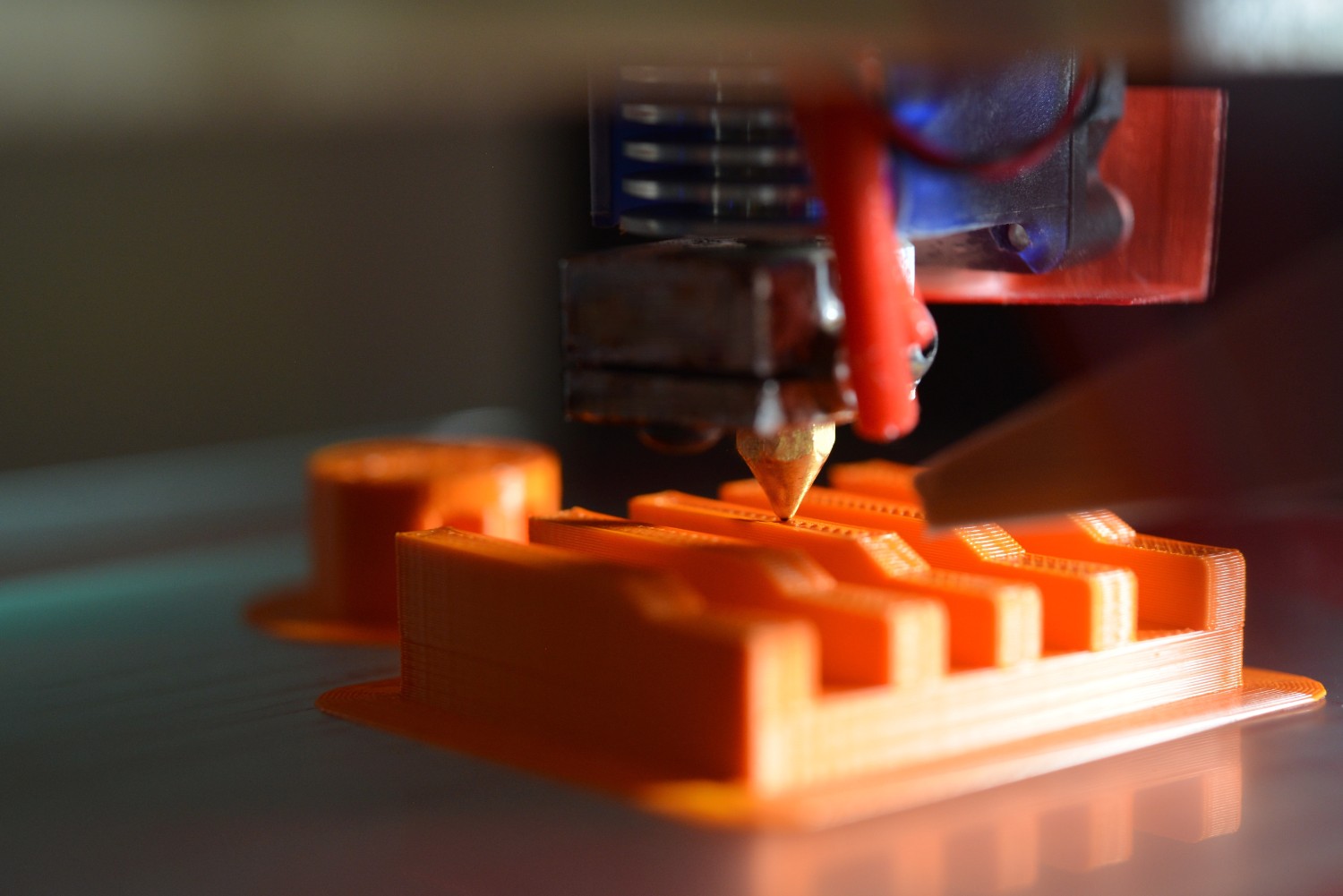
3D printer at work (Photo by Gavin Allanwood on Unsplash)
Our engineers and technicians take pride in their work and in how they can make our operations and maintenance even more efficient. And, naturally, they like to use innovative techniques, such as 3D-printing, to make their work easier. They work together with operations to get things done efficiently. This includes using 3D-printing for prototyping and manufacturing small numbers of unique parts.
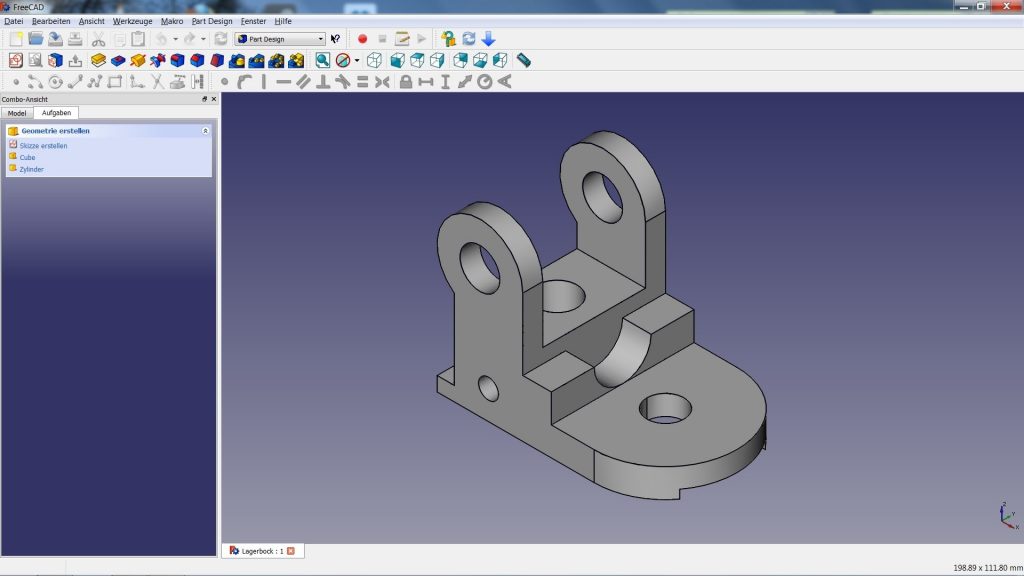
3D CAD drawing (Source: https://i.materialise.com/)
Practical 3D-printing applications
Many of our technical installations are designed and made especially for our car parks, take the QR code reader, for example. Our engineers make a test installation to find out what works best. Naturally, they 3D-print mounts to test the ideas and designs. When they’re happy with the setup, they decide how best to source the items.
Some things in car parks get damaged on occassion which means we have to carry out repairs. Our engineers have developed and 3D-printed their own jigs and templates so these repairs can be made quickly and efficiently.
Sometimes we need to add equipment to an existing cabinet. These items all need good ventilation so cannot just be bolted to the side panel. Using CAD software we can design a support bracket that meets our specific requirement for strength, weight and ventilation. We then 3D-print a prototype and check its usability. Adjustments are easily made and when we’re happy we can produce the exact number of brackets required.
Depending on the numbers of parts needed, we may print ourselves or order from a local third party.
Benefits all round
Using locally sourced 3D-printed parts is not only good for Q-Park, it’s also good for the environment.
There is little to no waste with 3D-printed parts, because we only make or order exactly what we need.
3D-printed parts do not have to be solid and so are light-weight. No material is wasted, unlike when a piece is milled or turned in metal, and unused 3D-print material can be recycled.
Parts are available quickly, because we either make them ourselves or order from a 3D-printing specialist locally.
We minimise logistics costs because we don’t order more than we need and we don’t have to wait for a shipment of standard parts to arrive from afar.
All this contributes to keeping our carbon footprint as small as possible.